为中国市场本土化德系测试体系
DENZA腾势在测试阶段的研发车辆已经超过100辆,进行了超过120万公里测试。腾势的整车测试涵盖了耐久实验、腐蚀实验、车队实验、环境适应性实验、碰撞实验。测试的地点是遍布在中国8个不同气温环境的城市,比如低温、高温、湿热、灰尘等不同的路面去做实验。
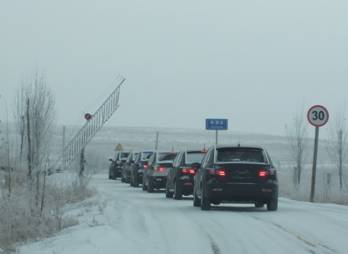
作为一款正向设计的电动汽车,腾势需要从零开始定义测试标准。为此,DENZA腾势的测试不仅要依照奔驰德国的标准保证品质。在整个研发过程中,戴姆勒在德国总部的工程师远程参与车辆研发,并定期来到深圳进行测试模拟、测试准备工作和规格设计说明等项目研讨。
在测试流程方面,参照奔驰标准,腾势建立了自己的标准,并通过细化的安全验证方案来保证整车的安全。首先,从电池、零部件层级开始,每一个零部件都有一个技术标准,而每个标准都是通过中德双方去讨论决定,并通过边测试、边研发、边验证的动态测试方式,最终形成更适应中国市场的腾势标准。在验证环节,腾势也定期邀请奔驰德国的技术人员进行阶段性整车试验和路面试驾,对车的状态进行整体评价,并对前期发现的问题进行验证,从而对下一轮测试提供输入。

为了更好的兼顾适应中国市场和保持戴姆勒品质,在整车的设计和测试上,腾势针对中国市场设定整车设计初始值,保证整车重量、整车操控性等方面适应中国市场特点。同时为保证验证的精确性,将初始值数据送往奔驰在德国的实验室进行仿真测试,并在德国标准的基础上做本土化改进。而在道路测试项目上,虽然测试团队不可能把德国的路搬到中国来,但他们通过采集德国的路谱系,在中国找一个类似的路,按照德国的标准去做实验。
引导建立行业标准的碰撞测试
2014年7月,腾势按照C-NCAP的碰撞标准,得到了五星成绩。而作为国内第一款进行这一测试的电动汽车,DENZA腾势也在建立着电动汽车的碰撞安全标准。
在碰撞测试中,由于电动汽车的车身较沉,撞击时的能量较大,达到测试标准很难。而腾势为自己定的测试标准是碰完的电池包拿出来,还能正常使用。为此,在戴姆勒仿真、碰撞安全尖端技术的支持下,腾势研发团队为电池提供保护的铝合金框架结构经过了几轮优化,包括碰撞、仿真、结构设计等。
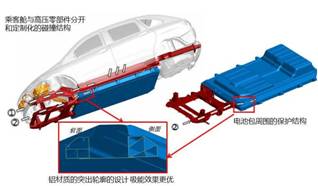
传统汽车吸能更多靠前舱,腾势则不同。它的底盘位置是外面包裹着铝合金框架结构的电池托盘。这一特殊的电池托盘设计为达到更优的能量吸收和碰撞力传导路径创造了条件,是整车碰撞安全理念的一部分。它能够传导不同方向的撞击力,并通过变形吸收能量,保证这些碰撞不会伤害到内部电池单体。
另外,在国标要求之外,腾势还按照奔驰在欧洲的标准加入侧柱碰,模拟实际撞车发生时车辆碰到一棵树或者电线杆的情况。在测试中,侧柱撞击了腾势车身中部的重量集中点,电池没有被损伤。电池托盘吸收了所有的碰撞能量,而且车身在撞击后没有前后歪斜,显示出腾势车身设计近乎50:50的前后配重,是良好操控性的保证。
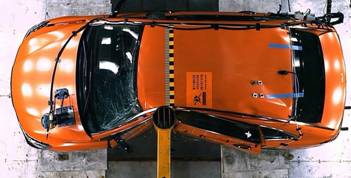
作为第一款按照C-NCAP标准进行碰撞测试的电动汽车,腾势解决了很多新的行业性安全课题。例如,目前只有传统的燃油车的碰撞测试评分指标和程序,但是怎么监控电动汽车的电流在碰撞的过程当中的情况?腾势使用了电能安全监测手段,测试电路各个节点在碰撞测试中的有效工作情况。通过跟相关机构的合作,这些实践将会引导整个行业在这个领域中的探索。
|